P6-Auditor helps find users who made mistakes in P6
Deleting and editing global data happens; P6-Auditor can help
Written by Nicole Jardin
Client Overview
Large Electrical Utility with several P6 databases with internal and external scheduling teams needed a way to manage and report on functions inside P6.
Challenges
-
With a large team of P6 users, it is hard to track down when projects are deleted
-
Ensuring that the EPS does not get changed when users are cutting and pasting projects was a challenge
-
When managing a resource pool of over 10 thousands crews, making sure your resource dictionary is maintained and coding kept up to date with more than one admin can be error prone
Results
-
Tracing project deletes easily and rollbacks if required
-
Reporting on update frequencies - actual starts, actual finishes, and percent completes
-
Edits to the resource dictionary that were not expected including deletes and cut and pastes
-
Verifying changes to activity codes and who made them as well as when they were made
-
Tracing EPS moves that no user admitted to
-
Finding logic changes that should not have been made as well as task deletes
Primavera P6 Case Studies
on Wednesday, 24 March 2021.
Posted in Case Studies
Integration allows PMs to manage 20 projects at once
PMs get on top of projects with daily integrated system
Written by Nicole Jardin
Client Overview
Calgary pre-fab manufacturer with international projects needed integration to accounting and purchasing system to get control over client commitments and internal and external spending for hundreds of simultaneous projects.
Challenges
-
Tracking costs to date on hundreds of projects manually was too time consuming
-
Client forecasting was taking too long and overruns were being missed
-
Senior management was not getting the reporting done in a timely manner
Results
-
Integrated daily costs from Discoverer into P6 and PCM Contract Management
-
Updated the external contract and PO costs into expenses
-
Integrated the internal detailed resource costs into resources and forecasted onto the budget resource
-
P6-Calculator did all the cost rollups and comparisons to the budget
-
P6-Calculator flagged integration errors, mismatches, and potential incorrect charges for the PM
-
BI Reporting was developed for cost to date, forecasting, earned value, CPI, SPI and changes to-date
Integrations Case Studies
P6-Calculator Case Studies
Manufacturing Case Studies
P6-Calculator News Articles
P6-Reporter News Articles
on Wednesday, 24 March 2021.
Posted in Case Studies
IT Portfolio Streamlined with PeopleSoft and P6
8 weeks to develop integrated system
Written by Nicole Jardin
Client Overview
The client is a large cancer research hospital in California. They use Primavera tools for portfolio and project management across the program management, IT and capital projects teams. The IT team was finding that the system was not giving them the project status and resourcing information they were hoping for. Nor could they ascertain what the resourcing, in-house and outsourced, capacity and efforts were for the short and long-term planning.
Challenges
-
Developing a new project management structure with new projects, upgrade projects and ongoing support work
-
Transparency for resourcing across multiple departments - reworking of roles, resource codes, employee ID from PeopleSoft
-
Overhauling the EPS, OBS, CAS, and WBS templates after completing workshops
Results
-
Led design sessions for changes to global structures, stage gate templates, and consistent deliverables
-
Remapping and migration was done with P6-Loader after each working session so management could see the changes right away
-
Training was delivered by Emerald using custom developed UPK content and small working sessions for the different business leaders and then team project managers
-
Management Dashboard for timesheet submissions, project stage gate and milestones from templates were developed
Custom Training Case Studies
Integrations Case Studies
Program Management Case Studies
Primavera P6 Case Studies
on Tuesday, 23 March 2021.
Posted in Case Studies
Oil exploration company uses P6-Loader to migrate to Primavera P6 with speed and consistent data.
Proactive Not Reactive Portfolio Planning
Written by Nicole Jardin
Client Overview
Client is involved in the exploration, development and production of crude oil and gas in Colombia. They had numerous drilling projects that were being managed principally from SAP with difficulty.
Challenges
-
SAP was providing data too late to effectively manage projects
-
Spending overruns were common
-
Rig planning and completions forecasting was not reliable
Results
-
Implemented P6 for planning the drilling program
-
Migrated from SAP report into P6 - used the P6-Loader to load in projects, WBS, and costs
-
Easy visualization and comprehension of the plan in P6
-
Consistent templating of data across the portfolio
-
Saved weeks of data entry
Primavera P6 Case Studies
on Monday, 22 March 2021.
Posted in Case Studies
Oracle E-Business EAM Integration to P6
Global Production Management with P6
Written by Nicole Jardin
Client Overview
As Canada's largest potash mining organization with over 20 mines in North America, managing global production supply is critical. Planning daily production, weekly short outages and monthly maintenance days while implementing larger capital projects and major shutdowns is very challenging. Using spreadsheets and lists was not working particularly well for production planning and productivity analysis in real time.
Challenges
-
Consistent coordination of Shutdowns and Capital Projects in short work windows while maintaining production and productivity forecasting
-
Detailed scope planning and resource planning across underground and above ground skilled resources
-
Easy updating, forecasting and realtime earned value analysis during the shutdown work and contractor productivity
Results
-
Realtime updates from Oracle E-Business EAM into P6 for Projects, Work Orders, Tasks and Resources allowing for easier plan development for maintenance work, mini-outage work, turnaround work windows and capital programs across several plants
-
Implemented within 6 months including dev, test, QA, and production. P6-Loader was used to move the P6 coding structures, EPS, OBS, codes, UDFs, and resources in a matter of minutes and to maintain these environments.
-
Better analysis of planned resource requirements, spending planning and timeframes across the capital programs throughout the plants
-
Improved delivery on outage deadlines, timeframes and what-if capability particularly related to managing production capacity across the plants
-
Better understanding of mining equipment and productivity rates for improved forecasting. Reduced effort to build the schedules, allowing better management of the short 1-2 power outage windows.
-
P6-Calculator ensured auto-archiving of the projects and work orders to keep the P6 database clean and manageable and to produce rollup data for resources and flagging of integration changes
Integrations Case Studies
Program Management Case Studies
P6-Calculator Case Studies
on Monday, 22 March 2021.
Posted in Case Studies
We integrated Aveva with P6 to drastically reduce the time our client spent updating their capital projects
Simplifying Engineering Updates
Written by Nicole Jardin
Client Overview
One of Canada's many potash companies runs all their capital projects with Primavera P6. With one scheduler on the team, it is difficult to keep up with the dozens of projects on the go to ensure monthly reporting is accurate.
Challenges
-
Updating some 20+ projects in P6 was time consuming at the end of each month
-
Mid-month reporting was not easy to do without spending extra hours to get all the updates into P6
-
Going over the updates with the extended team took a lot of coordination to schedule with so many people with different schedules
Results
-
Integrated documents statuses from Aveva
-
Templated the different task types and package types with preset calculation methods
-
Documents planned, in progress, completed, deleted
-
Set the start dates of tasks in progress, updated the percent completes and flagged changes to the tasks
-
Updated the resources - actual labor units
Integrations Case Studies
on Sunday, 21 March 2021.
Posted in Case Studies
Large oil and gas company uses P6-Loader to develop turnaround plans.
Moving to consistent processes and reporting
Written by Nicole Jardin
Client Overview
Large oil plant in Australia needed a more efficient way to develop their turnaround plans. This was typically being done by an outsourced engineering and contractor joint venture every 2 years. So each time different processes and team members were working with different methodologies.
Challenges
-
Struggling to build detailed schedules since they had to pull data from internal systems and contractor inputs and remap the data into standard template formats
-
Working with contractors during the turnaround providing updates in different ways
Results
-
Streamlined data imports by over 30%
-
Drastically reduced manual data entry by 50%
-
Improved standardized reporting during the planning stage and execution
-
Expanding P6-Loader’s use into other groups to improve the usage of P6
From Our Customer
We saved 6 weeks on our planning process, and were able to get feedback more quickly after using P6-Loader.
on Sunday, 21 March 2021.
Posted in Case Studies
Used the P6-Loader to move a client to the Primavera Cloud in two weeks.
In 2 weeks - all projects were ready
Written by Nicole Jardin
Client Overview
Project Management specialist overseeing a large building remediation program after Hurricane Sandy needed to move from on-premise P6 program development to the Primavera Cloud to share schedule information with Contractors and Owners Representatives.
Challenges
-
Setup a new P6 environment in the Primavera Cloud within 2 weeks
-
Transfer all P6 program data for over 750 projects in a standalone PPM database
-
Over 400 baselines needed to be moved as well
Results
-
Emerald provided P6-Loader aaS
-
Enterprise Data: built and loaded for EPS, OBS, Users, User Profiles
-
Global Data: merged and cleaned up while loading over 400 Resources and 50 Calendars
-
Project Data: 756 projects, 455 Baselines, 265,802 activities. Activity codes, resource assignments, and relationships were all transferred.
-
Approach - used a combination of XER and P6-Loader functionality
-
Saved weeks of manually re-creating global data, users/profiles, and baseline management. Went live 1 week after getting files.
Program Management Case Studies
on Sunday, 21 March 2021.
Posted in Case Studies
Large Australian rail company uses the P6-Loader to integrate SAP to Primavera P6.
Monthly cost loading made easy for hundreds of projects.
Written by Nicole Jardin
Client Overview
Large railway projects need a tremendous amount of coordination and strong scheduling. Managing monthly costs and updates from several regional contractors so that shareholders can be informed of status can be a challenge.
Results
-
Streamlined the efforts of updating down from 4 person weeks to 2 person days. Data Imports by over 30%.
-
Errors and mismatches were reduced significantly
-
Several macros made this extract and upload much more reliable than manual inputs
-
Reloading every day during the update window was smooth
From Our Customer
SAP to P6 updates were easy to perform so that forecasting was much more accurate.
Integrations Case Studies
Transportation Case Studies
Primavera P6 Case Studies
on Sunday, 21 March 2021.
Posted in Case Studies
The daunting task of cleaning up 10 years of projects was made easy with P6-Loader so archiving, cleaning, fixing and upgrading could happen.
P6-Loader made it easy
Written by Sue Hopkins
Client Overview
The client is a large Canadian producer, transporter and marketer of natural gas, oil and natural gas liquids. They use P6 for many project controls functions including their capital program. After years of working in a P6 database they wanted to move to a clean P6 environment.
Challenges
-
Their IT department needed assistance in Upgrading and Migrating Major Projects and Facility, Engineering and Construction databases to a new environment
-
Their Security Profiles, User and Global Data, some of which were corrupt needed to be cleaned up prior to move to new environments
-
Move large live projects with up to 100 baselines to the new environment in a short amount of time while users were not active
Results
-
Databases edited and cleaned up prior to migration including Security Profiles, User and Global Data, some of which were corrupt, using the P6-Loader tool
-
Archived old projects in place and moved over 400 projects and baselines to a new environment with only one weekend of down time
-
Migrated data was validated and compared to previous database to ensure all data was moved accurately
-
Saved hundreds of hours of manual work
Primavera P6 Case Studies
on Thursday, 17 December 2020.
Posted in Case Studies
Fiscal year budgeting is easy with PCM-Loader. Build or rework in Excel and load it up.
program reporting success
Written by Nicole Jardin
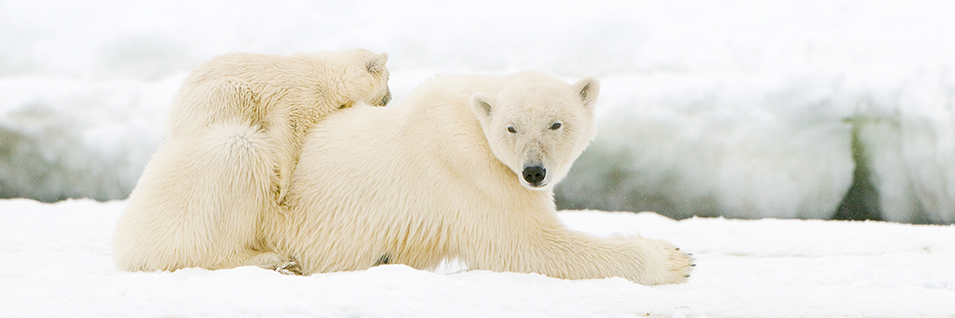
Client Overview
San Diego Unified School District is the second largest school district in California with an operating budget of over $1 Billion per year and serves more than 130,000 students in pre-school through grade 12. The district was a long time user of Primavera P6 and Primavera Contract Management, which were used to manage their construction and maintenance projects.
Results
-
Loaded in all the budgets within a few days
-
Easily reloaded the budgets when changed
-
Saved hundreds of hours
-
Reporting was correct and reliable
From Our Customer
“[We have] all of the budgets established using the PCM-Loader and that’s been a big help.”
- Joel Splittgerber, Program Controls Manager
Program Management Case Studies
on Wednesday, 16 December 2020.
Posted in Case Studies
Integration enables the management of work orders, tasks, relationships, resources, and resource assignments; providing synchronized scheduling and resource updates.

Emerald Associates created Work Orders from SAP Hana Cloud into P6 Azure Cloud for detailed task and resource management in P6 using Mulesoft and
the EAI P6 Cloud API. We created SAP Operations and supporting resources and resource limits as new resources are introduced in SAP.
- WBS - create/update SAP Operations into P6
- Tasks - create/update tasks from SAP operations
- Relationships - create/update relationships from SAP and allow P6 schedulers to change and update them back from P6
- Resources - create/update for new crews in SAP and set limits
- Resource Assignments - create/update resource assignments from SAP operations and sub-operations for detailed resource management
- P6 → SAP - return operation and sub-operation lists and relationships to update SAP with P6 schedule information
- Return task lists generated in P6
on Thursday, 15 June 2023.
Posted in Case Studies
Integrating capital projects and maintenance work orders from Maximo to P6 allows detailed planning and resource management within P6.
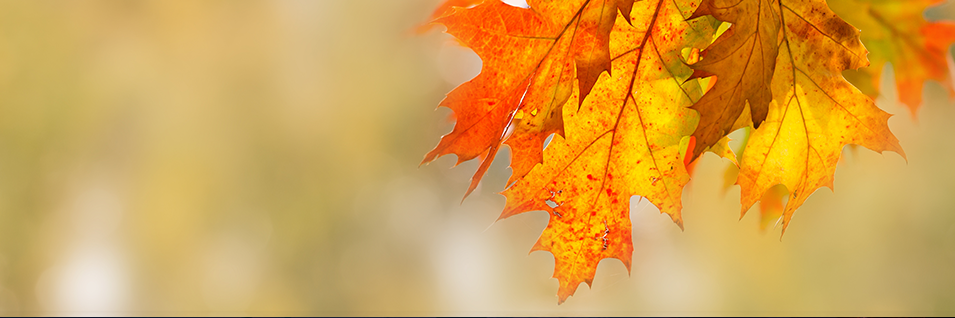
Integrating capital projects and maintenance work orders from Maximo to P6 using Maximo IFACE tables and
EAI P6 Cloud API to allow detailed planning and resource management within P6. Create new tasks from P6 via Maximo Web Services when schedulers needed to add additional supporting tasks to the schedule and update tasks from P6 to Maximo via Informatica when the tasks are scheduled in P6.
- Projects - creating/update projects using a standard P6 template by geography and project type
- WBS - create/update work orders in weekly maintenance planning and yearly project planning. Update statuses
- Tasks - create/update/delete from work order tasks developed by engineering
- Resources - create/update resource crews as new ones are added to Maximo
- Resource Assignments - create/update resource assignments from Maximo. Allow P6 team to control hours as needed
- Steps - update summary data from work orders on summary tasks in projects for easier reporting and management
- P6 → Maximo - allow P6 to create tasks in Maximo for certain work types and update project start and finish dates
on Thursday, 15 June 2023.
Posted in Case Studies
Large Pre-Fab Manufacturer uses P6-Loader to get control over their planning, scheduling and cost controls.
competing priorities resolved
Written by Nicole Jardin
Client Overview
Calgary pre-fab manufacturer with international projects needed to get better control over the planning, scheduling and cost controls of several hundred projects on the go at once for wide ranging clients.
Challenges
-
Fabrication team was swamped and priorities were unclear
-
Change orders were impacting priorities
-
Needed a common approach to planning 250 projects on the go
Results
-
Used the P6-Loader to develop P6 Structures - EPS/OBS/Cost Accounts
-
Fully templated program
-
Cost Loading Changes with Overhead, Profit tracking
-
Daily Costing Reporting
Manufacturing Case Studies
on Wednesday, 16 December 2020.
Posted in Case Studies
Integration between PIMS and Primavera P6 ensures quality compliance reporting for large electrical company.
compliance reporting made easy
Written by Nicole Jardin
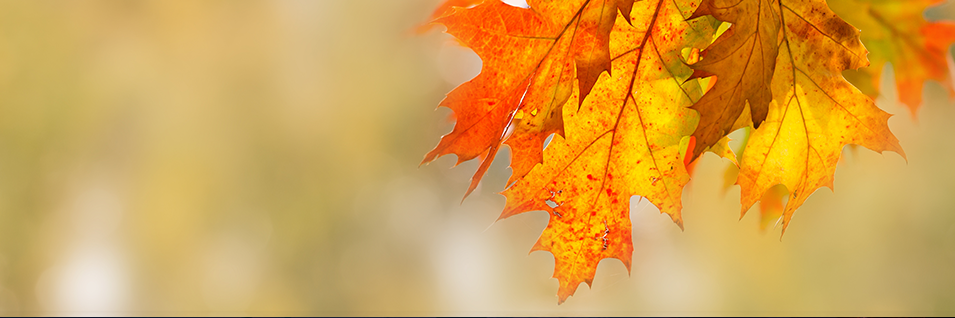
Client Overview
Supplying Electricity to clients throughout Alberta requires strong program management. Ensuring that all regulatory reporting is complied with in multiple jurisdictions with differing rules and requirements can be a challenge.
Challenges
-
Ensuring regulatory reporting compliance was up-to-date and accurate on a daily basis let alone for monthly reporting
-
Managing changing conditions was difficult to ensure all stage gate reporting reflected these changes
Results
-
Integrated to PIMS key milestones for stage gates
-
Ensured consistent reporting - and reduced errors significantly
-
Automatic integration on project creation with templates with estimate dates
-
Within 4 weeks system was running
-
Cloud and on-premise integration
Integrations Case Studies
on Wednesday, 16 December 2020.
Posted in Case Studies