TAPS - Not Just for Turnaround Schedules
Below is just one of a large number of scenarios for how TAPS can be used.
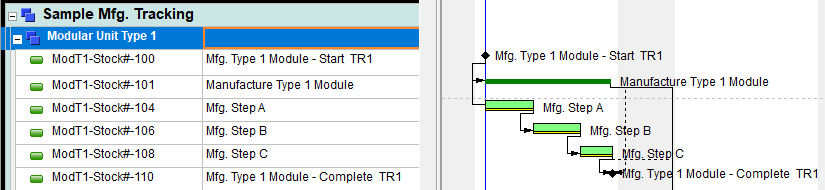
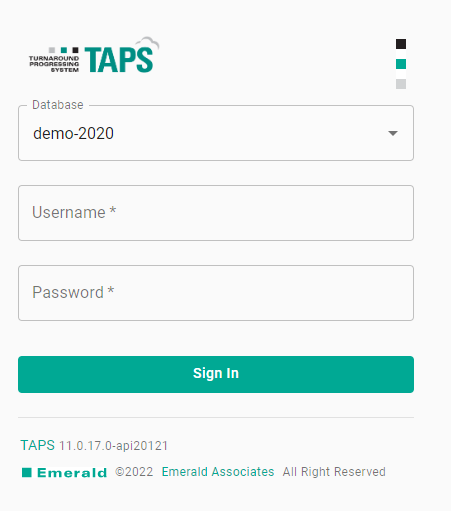
Login to TAPS and update schedule progress. Progress your scheduled activities as they are completed in the production process. Track/identify your line items using a barcode scanner and barcode ids on the line items or paperwork for the line items. Update the activity status for the line items using TAPS, and the production line progress is reflected in the production schedule.
Equip your team with self-serve dashboards that are available using P6-Reporter (previously EP-datawarehouse). As updates are completed to the schedule using TAPS, schedule snapshots are taken regularly using automated snapshots. You control the interval for the automatic snapshots to be created, and they update the information in the self-serve dashboards in P6-Reporter. Your team now has quick, easy-to-digest, and current information available in the self-serve dashboards in P6-Reporter. For comparison, you have previous snapshots as well as current snapshots available for reporting. Perhaps steps were taken to address an issue on one production line and you are looking to confirm the steps have addressed the issue – self-serve dashboards give you easy access to current information on that. If there are members of your team that do not need to directly access P6 as a scheduling tool but do need to access the information generated by P6 schedules in an easy-to-digest and easy-to-access format, then TAPS and P6-Reporter have it covered.
About the Author
Mary Lynn Backstrom, PMP, PMI-SP, PMI-BA – Implementation Specialist
Mary Lynn spent many years filling a variety of project controls duties such as planning, scheduling, analyzing, training and continuous improvement in the Aerospace Industry. Since joining Emerald in 2008, she has been a tremendous asset to the Emerald team. She has worked as a lead scheduler for turnarounds, led sessions for review and troubleshooting of scheduling and reporting, created and given custom training courses for clients, and is a sought after Primavera P6 trainer.
Mary Lynn enjoys some very diverse spare time activities. Along with a variety of outdoor activities such as gardening, she also enjoys making life size lawn ornaments for special holidays like Christmas. Mary Lynn is known for her participation in the community as well. You may have seen her walking in fundraisers in Edmonton and Calgary for the Cancer Society.