Emerald Helps Midstream O&G Client to Upgrade P6 and Clean Database with P6-Loader SaaS
Emerald Helps Midstream O&G Client to Upgrade P6 and Clean Database with P6-Loader SaaS
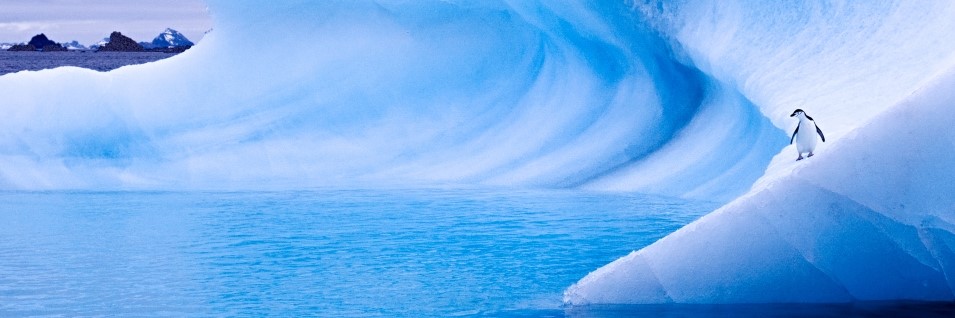
Client Overview
Client is one of the largest midstream oil and gas operators in Canada. The company services oil and gas producers in Western Canada and transports natural gas liquids to markets throughout North America.
Challenges
-
Client required their Primavera P6 database to be upgraded to v21.
-
Along with the upgrade, areas were identified where data needed to be cleaned up.
-
P6 security is a little different in the new version of P6, and the client asked for assistance with security for P6 users in the new P6 version.
Results
-
The database upgrade was completed.
-
The P6-Loader was used to review the data for potential areas of clean-up. The P6-Loader Usage Reports provided a quick and consolidated summary, so we were able to clean up UDFs, codes, and calendars.
-
We reviewed the security in the new version and addressed the option selections in security profiles and made sure they were set up correctly.
Primavera P6 Case Studies
on Wednesday, 06 December 2023.
Posted in Case Studies
Learn how large energy company uses risk analysis
Client Overview
The client referenced in this case study is a Canadian integrated energy company that is based in Calgary, Alberta, and is considered one of Canada's largest energy companies, as well as having been previously ranked as one of the top 50 biggest public companies in the entire world. The refinery based in this case study began refining crude oil in 1955. The refinery produces a full range of refined petroleum products that includes gasoline, distillate, heavy fuel oil, solvents, asphalt and petrochemicals. It is also a leading producer of petrochemical products.
Challenges
-
The project was underway, but there was debate as to whether it was required because of a merger.
-
There was a lot of uncertainty around the project budget.
Results
-
The analysis showed that the project would cost significantly more than the budgeted amount.
-
The analysis showed that the project would be later than scheduled.
-
As a result of the risk analysis, the project was cancelled.
on Sunday, 11 June 2023.
Posted in Case Studies
Discover how this refinery used TAPS to improve the accuracy and speed of progress data entry during their turnarounds.
Turnaround progress entry more efficient and streamlined at the refinery
Client Overview
The client is an evolving energy company with an enduring family of brands. From refining to midstream to marketing, they provide traditional and renewable fuels and lubricants for planes, trains and automobiles – plus other essential products such as asphalt, roofing tar and components for medicines and cosmetics.
Challenges
-
The refinery needed a way to streamline their data entry and schedule updating.
-
Manual data entry of progress after each shift was taking two schedulers 4 to 5 hours to complete, which took time away from the analysis of their updated schedules.
Results
-
Schedule updates now take a matter of minutes using bar code scanners, rather than several hours.
-
The time saved using TAPS freed up schedulers' time to analyze the results and provide better reports to management after each shift.
-
Primavera P6 updates are now more accurate.
on Tuesday, 04 April 2023.
Posted in Case Studies
Learn how Emerald helped an oil refinery prepare for a turnaround using Primavera P6
Refinery used P6-Loader to create a P6 schedule prior to a turnaround starting
Client Overview
The client is one of the largest refineries in Canada. They were using CASP as their project management solution for their turnaround (TA). They moved to P6 EPPM six months before their TA and needed to get the historical data from CASP into P6 without delay while getting the team up-to-speed on P6.
Challenges
-
Previous turnarounds did not finish on time and on budget and were hard to manage.
-
They had more than 1000 work packages planned, but they were in Excel or on paper.
-
They had no schedulers familiar with P6.
-
Time was short - Emerald was put on the project only 6 months before the turnaround was starting.
Results
-
Emerald sent two implementation specialists four months before the TA started. They set up P6 and created a resource-loaded CPM schedule.
-
Used P6-Loader to automate grabbing simple Work Order, Task, and Resource sheets from Excel to create the P6 schedule. More packages were being developed and loaded right throughout the turnaround.
-
A full critical path schedule was built, resource leveling was developed, and reporting and metrics were standardized.
-
Emerald helped run their three subsequent TAs.
-
Utilized TAPS for updating progress of the activities.
Primavera P6 Case Studies
on Monday, 23 January 2023.
Posted in Case Studies
Learn how TAPS helped with a successful turnaround
Refinery used TAPS to run a successful turnaround
Client Overview
Beginning operations in the early 1900s, the client in this case study is now one of Canada's largest oil refineries and a major supplier of Canada's fuel, distributing millions of litres of fuel a day, and playing a key role in the Canadian energy sector. The complex has undergone various upgrades and expansions over the years to enhance its processing capabilities and efficiency, including a $2.9 billion upgrade project in 2012 that increased operations up to 145,000 barrels per day.
Results
-
Successfully ran a $60M turnaround.
-
Gave them more time to focus on analyzing the schedule.
-
Less licenses of Primavera were required for updating progress.
-
They didn’t require a scheduler for updating progress and were able to use a summer student instead.
From Our Customer
“We never worry about the accuracy of the updating progress in P6.”
on Thursday, 19 January 2023.
Posted in Case Studies
P6-Auditor helped a large oil company recover from P6 data loss
Report on P6 Data Changes
Client Overview
The client is a Canadian integrated energy company that specializes in the production of synthetic crude from the oil sands. They have been a pioneer in the development of technologies for oil sands extraction and upgrading processes, and are considered a prominent player in Canada's energy sector.
Challenges
-
Resources and code dictionaries were being incorrectly modified in the Primavera P6 database
-
Projects were being removed from the database
-
EPS nodes were being moved out of place
-
Uncertainty about how their licenses were being allocated across multiple databases
-
Identify users who needed training and guidance on how to properly use Primavera P6
Results
-
Focus training on users who needed it
-
Determine active users in Primavera P6 and license distribution
-
When a deletion of activity code types occurred, company was able to recover quickly from the data loss
Primavera P6 Case Studies
on Tuesday, 27 July 2021.
Posted in Case Studies
One refinery using TAPS and P6-Loader saw great improvements in speed and accuracy when working with P6 data that the company rolled out the tools to all refineries.
Simplify the STO process from beginning to end
Client Overview
Client is an oil and gas company with a focus in refining and marketing petroleum products, processing natural gas and gas liquids, and manufacturing petrochemicals, polymers, and plastics.
Challenges
-
The Planners wanted to add information to their schedules in an easy way using information provided in spreadsheets.
-
The Washington state refinery was seeking to simplify and accelerate the input of progress.
-
The contracted master scheduler at the Ferndale Refinery had used P6-Loader and TAPS before and knew the tools would simplify their STO processes.
Results
-
TAPS was initially used at the Ferndale Refinery and saved so much time, it is used on turnarounds at all the company’s refineries now.
-
After using P6-Loader at the Ferndale refinery, the tool was purchased company-wide for use with all P6 databases.
on Thursday, 17 June 2021.
Posted in Case Studies
TAPS helped turnarounds run smoother and with less stress.
Scanning made all the difference
Client Overview
As an international integrated Oil and Gas organization from Vienna, Austria, previously listed as one of the 500 largest public companies in the world, large turnaround projects are second nature; however, getting updates and forecasting done is still a challenge.
Challenges
-
Updating thousands of activities within 2 hours of a shift change.
-
Ensuring a simple forecasting at the end of the shift to get the next crew lead to status this to complete.
-
Knowing what inspections were needed.
-
Getting the crews to the right place for efficiency.
Results
-
The New Zealand group got TAPS at the recommendation of the Engineering leads, and this has been great for them. With TAPS, the updating process was much more smooth and painless.
-
The team had a lot less stress to deal with, and reporting was simplified.
-
Accurate forecasting went up significantly.
-
The turnarounds have been smoother on the impact analysis.
-
Better mitigation of work area access.
on Tuesday, 08 June 2021.
Posted in Case Studies
Discover how Suncor Energy harnessed Emerald Associates' TAPS to reduce their scheduling costs while boosting their speed.
TAPS makes updating faster and easier
Client Overview
Suncor Energy is a Canadian integrated energy company based in Calgary, Alberta. It specializes in the production of synthetic crude from the oil sands.
Challenges
-
Updating schedules was incredibly slow
-
Updating schedules was inaccurate
-
The schedulers they had to hire were expensive and in high-demand
-
Early shifts were needed to get updates in on time
Results
-
3x faster progress entry into schedule
-
Updating schedules was much more accurate and efficient when the human component was taken out
-
Less skilled resources could be used - can use entry clerks and foremen instead of the more expensive schedulers
-
A lot of money was saved
-
Decided to implement TAPS throughout their multiple refineries
From Our Customer
“We have used this system for progressing Primavera scheduled activities for three turnarounds now, and I and everyone who has used it for updating are most favorably impressed with the speed and accuracy achieved. What used to take an experienced user 1½ to 2 hours to update manually, can now be done in ½ to ¾ of an hour and can be done accurately by a less experienced user.”
on Monday, 31 May 2021.
Posted in Case Studies
Project Managers do some of the heavy-lifting to lighten the project controls team workload.
Weekly updating of OPEX and CAPEX projects in an Operational Plant
Written by Nicole Jardin
Client Overview
When you are working in an operational plant with daily maintenance, small upgrade projects and major expansion capital projects all going on at once, it is critical to manage schedule inter-dependencies and potential impacts so that nothing goes off the rails.
Challenges
-
Reporting weekly progress and monthly costs to date on over 50-100 projects
-
Reviewing inter-dependencies, schedule impacts, and coordinating crews with area holds
-
Balancing the project controls teams' overtime each week and at the end of the month
-
Ensuring interproject critical path analysis was done
-
Getting updates from remote engineering firms in different time zones
Results
-
With CAPPS, weekly status updates were done by the project managers and submitted to the project controls team for approval in P6
-
Monthly cost updates and forecasting of EAC were done by the project managers and submitted to the project controls team for approval in P6
-
Key management milestone reporting was streamlined significantly
-
Project controls teams were freed up to deal with larger turnaround projects
-
Project controls teams were able to focus on P6 re-scheduling and critical path analysis
on Thursday, 29 April 2021.
Posted in Case Studies
Learn how this refinery used P6-Loader and TAPS to improve accuracy and speed when working with data in their P6 schedules and how they used EP-datawarehouse and custom dashboards to help with cost control and management visibility for their turnarounds.
Cost controls more effective and schedule updating more streamlined
Written by Sue Hopkins
Client Overview
Client is one of North America's largest integrated energy companies. Their Lima refinery was looking for a way to improve their turnarounds and create custom dashboards for better visibility for management.
Results
-
Emerald's Turnaround Productivity Package - TAPS, P6-Loader, EP-dashboard, and P6-Reporter (previously EP-datawarehouse) was implemented
-
Schedule updates are now completed in less than a quarter of the time. Updating takes a matter of minutes using TAPS, rather than several hours
-
P6-Loader streamlined the addition of found work to both the working schedule and the baseline schedule
-
P6-Reporter is used to store snapshotted data for multiple uses for EV and Trending
-
EP-dashboards utilize the snapshot data to create custom dashboards for management including Green-Ups, Inspections and S-Curves
From Our Customer
"Coming in at 6am instead of 4am each day made a big difference to our team; not only on a daily basis but by not being exhausted at the end of the turnaround. TAPS saved 600 grueling hours.”
P6-Reporter News Articles
on Wednesday, 24 March 2021.
Posted in Case Studies
Oil exploration company uses P6-Loader to migrate to Primavera P6 with speed and consistent data.
Proactive Not Reactive Portfolio Planning
Written by Nicole Jardin
Client Overview
The client is involved in the exploration, development and production of crude oil and gas in Colombia. Their projects often involve upstream activities, including drilling new wells, enhancing production techniques, and managing existing assets. They focus on maximizing the value of their resources while maintaining efficient operations. They had numerous drilling projects that were being managed principally from SAP with difficulty.
Challenges
-
SAP was providing data too late to effectively manage projects
-
Spending overruns were common
-
Rig planning and completions forecasting was not reliable
Results
-
Implemented Primavera P6 for planning the drilling program
-
Migrated from SAP report into Primavera P6 - used the P6-Loader to load in projects, WBS, and costs
-
Easy visualization and comprehension of the plan in Primavera P6
-
Consistent templating of data across the portfolio
-
Saved weeks of data entry
Primavera P6 Case Studies
on Monday, 22 March 2021.
Posted in Case Studies
Large oil and gas company uses P6-Loader to develop turnaround plans.
Moving to consistent processes and reporting
Written by Nicole Jardin
Client Overview
Large oil plant in Australia needed a more efficient way to develop their turnaround plans. This was typically being done by an outsourced engineering and contractor joint venture every 2 years. So each time different processes and team members were working with different methodologies.
Challenges
-
Struggling to build detailed schedules since they had to pull data from internal systems and contractor inputs and remap the data into standard template formats
-
Working with contractors during the turnaround providing updates in different ways
Results
-
Streamlined data imports by over 30%
-
Drastically reduced manual data entry by 50%
-
Improved standardized reporting during the planning stage and execution
-
Expanding P6-Loader’s use into other groups to improve the usage of P6
From Our Customer
We saved 6 weeks on our planning process, and were able to get feedback more quickly after using P6-Loader.
on Sunday, 21 March 2021.
Posted in Case Studies
The daunting task of cleaning up 10 years of projects was made easy with P6-Loader so archiving, cleaning, fixing and upgrading could happen.
P6-Loader made it easy
Written by Sue Hopkins
Client Overview
The client is a large Canadian producer, transporter and marketer of natural gas, oil and natural gas liquids. They use P6 for many project controls functions including their capital program. After years of working in a P6 database they wanted to move to a clean P6 environment.
Challenges
-
Their IT department needed assistance in Upgrading and Migrating Major Projects and Facility, Engineering and Construction databases to a new environment
-
Their Security Profiles, User and Global Data, some of which were corrupt needed to be cleaned up prior to move to new environments
-
Move large live projects with up to 100 baselines to the new environment in a short amount of time while users were not active
Results
-
Databases edited and cleaned up prior to migration including Security Profiles, User and Global Data, some of which were corrupt, using the P6-Loader tool
-
Archived old projects in place and moved over 400 projects and baselines to a new environment with only one weekend of down time
-
Migrated data was validated and compared to previous database to ensure all data was moved accurately
-
Saved hundreds of hours of manual work
Primavera P6 Case Studies
on Thursday, 17 December 2020.
Posted in Case Studies